
WVM Kenic Static Mixers
Chemineer has designed and manufactured static mixers under the Kenics trade name for the water and wastewater industry for over 30 years. The first applications used the Kenics helical element KMS mixer, and this is still used widely today for pipes of 150mm diameter and less, for gas-liquid dispersion applications and where mixing is required at very low flow conditions.
In the early 1990’s Chemineer researched, patented and introduced a novel and unique type of static mixer that generated multiple vortexes to create highly energy efficient (low head loss) radial mixing effects. This mixer, which we called the HEVTM (High Efficiency Vortex) set the standard for ultra low head loss mixing. Over the last 12 years over 1000 full scale HEV mixers with diameters ranging from 50 to 2200mm and for open channels up to 6m wide have been installed worldwide in water and waste water plants.
The Kenics WVM mixer
Our market research showed us that the Kenics HEV mixer was liked by industry for two main reasons – its low head loss and its open, non blocking structure. On the other hand, the HEV requires relatively long and expensive injectors, and is not well suited to very low flow rate conditions. A project to build on the key advantages of the HEV but to be able to offer more a more flexible range of options more suited to differing flow conditions and with improved additive injection designs and lower construction costs was completed in 2002 and its performance validated by the BHR Group (1). The new range of mixers is called the WVM (Water Vortex Mixer). Three different WVM designs are now available. These allow the main project design parameters of length and pressure drop to achieve a certain CoV (2) within a certain time to be optimised:
- Specifications
- Technical Data
- Advantages
- Industries
- Documents
- Contact
Specifications
- Models: WVM A, WVM B, WVM C
- Injection Point: Simple wall additive injection
- Mixing Elements: Trapezoidal shaped elements
- Dimensions: Varies between models
- Performance Validation: Test data validated by BHR Group
- Flow Conditions: Suitable for low flow rates (0.1-0.3 m/sec)
Technical Data
Principles of Operation
In all Kenics® KM Series Static Mixers, a patented helical mixing element directs the flow of material radially toward the pipe walls and back to the center. Additional velocity reversal and flow division results from combining alternating right- and left-hand elements, thus increasing mixing efficiency. All material is continuously and completely mixed, eliminating radial gradients in temperature, velocity and material composition.
Mixing Applications
- Turbulent Blending: Produces rapid mixing by inducing circular patterns that reverse direction at each element intersection.
- Laminar Blending: Alternating helical elements continually divide, stretch, and reorient the flow stream to produce complete mixing with minimum pressure drop.
- Liquid/Liquid Dispersion: Uniform turbulent shear field quickly disperses immiscible liquids and produces a narrow drop size distribution.
- Gas Liquid Dispersion: Gases can be incorporated into turbulent liquids; mass transfer rates are dramatically enhanced.
- Extrusion: Thermogenizers available for blending thermal gradients, color, and additives.
Product Offering
- Sizes: 3/16″ to 120″
- Material: Carbon steel, 304, 316, Alloy 20, Monel 400, Hastelloy C-276 & B2/3, Titanium, Nickel 200, Inconnel 600/625, PTFE, PVC, CPVC, FRP
- Geometry: Limited to round pipe, tubing, or duct
- Retention Types: Welded, removable, edge-sealed
Advantages
- Simple Design: Wall injection point and optimized length vs. pressure drop parameters.
- Enhanced Performance: Better mixing at very low flow rates (0.1-0.3 m/sec).
- Cost Efficiency: Lower capital and operational expenditures (CapEx and OpEx).
- Validated Performance: Test data validated by an independent organization (BHR Group).
Industries
- Water Treatment
- Wastewater Treatment
- Chemical Processing
- Environmental Engineering
Documents
Contact our Process Equipment Team
- Stephen White - Mob: 083 165 3830
- Michael Bradley (External) – Mob: 086 047 6178
- Ross O’Donovan – Tel: 021 461 7230
- Tel: 021 461 7200
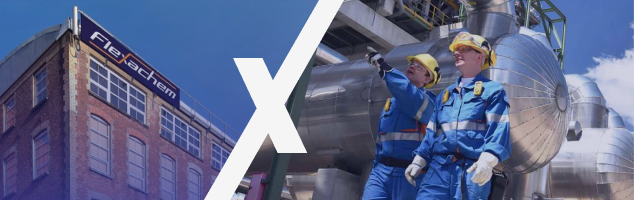
-
PumpsNETZSCH
Progressive Cavity Pump
-
PumpsFlowserve
SIHI SuperNova Pump ZDN – Hot Water
-
PumpsNETZSCH
Multi Screw Pump
-
PumpsFlowserve
Mark 3 Recessed Impeller Pump
-
Mixing TechnologyChemineer
Chemineer HS Turbine Agitators
-
Mixing TechnologyGreerco
Greerco Pipeline Mixers
-
PumpsFlowserve
Durco Mark 3 Pump – ANSI/ASME standard