Mixing Technology
In industrial process engineering, when we refer to “mixing technology” we are speaking about the various steps & process equipment involved in stirring liquids to cause turbulence which eventually results in agitating these liquids into a solution.
- View All
- Actuation
- Heat Exchangers
- Instrumentation & Control
- Mechanical Seal
- Mixing Technology
- Other
- Process Equipment
- Pumps
- Sight Glasses
- Software
- Steam Systems
- Tank & Pipeline Ancillaries
- Tank Venting
- Valves
Product categories
-
Mixing TechnologyChemineer
HT Turbine Agitators
-
Mixing TechnologyGreerco
Greerco Pipeline Mixers
-
Mixing TechnologyChemineer
Chemineer HS Turbine Agitators
In industrial process engineering, when we refer to “mixing technology” we are speaking about the various steps & process equipment involved in stirring liquids to cause turbulence which eventually results in agitating these liquids into a solution. Miscible liquids will only need light to medium agitation to mix, while ingredients such as powders or more viscous fluids will require higher levels of agitation to achieve a homogeneous mixture.
The Pharmaceutical industry will typically utilise a number of organic solvents, acids and caustic ingredients to enable a catalytic reaction that results in the end product through chemical interaction. The liquid mixing is via a reactor or blend tank and the aim is to allow all the ingredients to interact and produce a uniformly mixed product. This is then further processed through a filter dryer etc.
Another process is slurry agitation, a slurry is generally a liquid with higher levels of solids contained in it. In the Pharma sector, the solids would be the product / active ingredient which is then further processed via a filter dryer to leave the powder. In the waste-water treatment sector, a slurry will have higher solids content that is transferred for de-watering. A slurry agitator is often used to keep the solids in suspension to prevent settling out and forming on the base of the vessel or bulk tank before being transferred to the next stage of processing.
Flexachem provide a full range of mixing technology from leading brands across all applications from Tank Agitators, Slurry Agitators, Pipeline, Static Mixers, Colloid Mills, Homogenizers, Heat Exchangers, Glass Lined Tank Reactors, Cone type blenders and Filter Dryers to meet industry requirements.
Which type of Mixing Technology does Flexachem provide?
Flexachem provide solutions for all mixing applications via its supply partners. From lab scale to IBC to Bulk storage & across all market segments. We have dedicated specialists to support these partner applications in Ireland. We work with you to provide options that match your application, technology and budget needs.
These technologies handle all fluids viscosity ranges, shear sensitivity, full pH range and Electrical conditions. (Safe area/ ATEX).
Our brand partners include Chemineer, PRG, Inoxpa and Prodomix and cover every mixing application in industry.
Tank agitators come in the form of top mounted, bottom mounted or side entry. Pipeline or Static mixers are bolted inline and the fluids are pumped through them. Each type has a range of applications depending on the ingredients that are needed to be mixed and the type of mixing needed.
- Bottom Entry Magnetic drive units are used for aseptic mixing requirements of low viscosity liquids, typically in the biotechnology and high purity industries.
- Side Entry units are typically used for larger tanks such as milk silos or large diameter bulk tanks
- Top entry units are most common in tank mixing applications are come in a huge variety of scale & technology
- Static mixers are common in chemical dosing applications such as the water treatment sector where an open tab design is key to prevent blockage. Other designs such as a helical element & cross lattice are also common. Generally, do not use static mixers to mix powders.
The applications for tank agitators tend to fall under the following categories:
- Blending
- Heat transfer
- Homogenisation
- Reactor
- Suspension
- Storage
- Continuous reaction
- Fermentation
- Hydrogenation
Depending on the industrial sector the clients is in, the mechanical & material suitability for each application can differ greatly. Each of the applications have a typical impeller type that is suited to deliver the turbulence necessary to mix the ingredients.
What broader support for the customer is available?
Often clients want to get an idea of the performance of the agitator to reduce the risk of capital expenditure.
Flexachem have worked with a number of clients to provide both 2D and 3D Computer Fluid Dynamic (CFD) of the working conditions in the tank – areas that may not be mixing as well, dead spots and power draw of the agitator. Available to the client is information on models power draw, pumping capacity for multiple impeller types and sizes, analyses gas dispersion, ability to suspend solids & blend times. It also can provide mechanical design checks on shaft stresses, gearbox bearings and gear life
Ultimately, our client base are able to make a better informed decision on capital plant investment along with their own internal process engineering support. Often we are asked to model up existing performance and enhance it through updated design proposals.
If you have a question around our mixing technology range why not contact one of our product specialists to find out more.
Brochures:
Do you have questions or comments about receiving a quote, our products, solutions and services, and support? Contact us by filling out the form.
- Stephen White - Mob: 083 165 3830
- Michael Bradley (External) – Mob: 086 047 6178
- Ross O’Donovan – Tel: 021 461 7230
- Tel: 021 461 7200
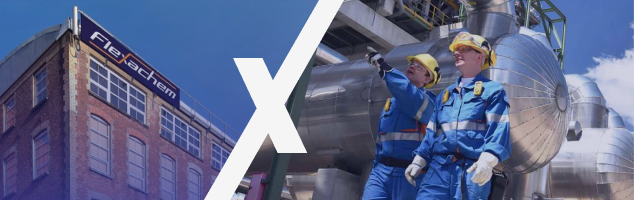