Glass Lined Reactor
In the chemical and pharmaceutical sector, a glass lined reactor is used given their compatibility with a wide range of chemicals. The reactor is a vessel with an agitator that allow the mixing of chemicals in a contained environment. The reactor can be pressurised and operate in a range of temperatures. The top section of the reactor allows the process nozzles to connect which bring in the chemicals and gases as appropriate and allow for cleaning head nozzles. They have a number of sizes but typically range from 63 litres to 16000 litres.
- View All
- Actuation
- Chillers
- Heat Exchangers
- Instrumentation & Control
- Mechanical Seal
- Mixing Technology
- Other
- Process Equipment
- Pumps
- Sight Glasses
- Software
- Steam Systems
- Tank & Pipeline Ancillaries
- Tank Venting
- Valves
-
Tank & Pipeline AncillariesInoxpa
Inoxpa Sauce Production Skid
-
Tank & Pipeline AncillariesInoxpa
Inoxpa Dairy Manufacturing Miniplant
-
Mixing Technology3VTECH
Vacuum Drying
-
Mixing Technology3VTECH
Nutsche Pressure Filtration
-
Mixing Technology3VTECH
3v Glass Types
-
Mixing Technology
Rectangular & “D” Ended, Elongated Sightglass, Series RSG & LSG
-
Mixing Technology
Circular Sightglass Fittings To DIN 28121 Or Similar
-
Mixing Technology
Circular Sightglass Fittings To DIN 28120 Or Similar
-
Mixing Technology
Chemlux Light fittings for Safe Areas KL/PL
How does a glass lined reactor work?
A reactor works by allowing the chemicals into a contained space and agitating them via the centrally mounted agitator. The vessel will typically have baffles included to ensure the sufficient level of turbulence inside to mix / blend the chemicals and enable the reactor. Normal chemical reactions take place given the correct catalysts present, the chemicals and pressure / temperature conditions and contact time. The end product could be crystalline or liquid.
What are the applications and uses of Glass lined reactors?
The primary use is chemical mixing and the variants are the pressure, temperature, gases used (hydrogenation / chlorination) and catalysts. Glass lined reactors are able to be cleaned to a high standard which prevents batch carry over.
What are the different types of glass qualities used?
The properties of the glass will allow for a few differing performances in the vessel. The type of glass can influence conductivity, thermal transfer and shock as well as a range of pH duties covering acidic / basic conditions. The glass can also have differing colour properties from transparent to white and light / dark blue as examples
Which glass thickness is used for glass lined reactors?
A guide thickness is 2mm which allows for the corrosion of via chemical reactions in the vessel.
What is the Spark Test in a glass lined reactor?
This is a destructive maintenance test that shows any condition of the glass and path to the vessel wall as a leak path. An annual test is recommended but this is dependent on the use of the vessel.
What are the different “types” of glass lined reactors?
There are 3 general reactor styles under DIN in line with the increasing volume per reactor. AE / BE / CE style reactors have differing volume capacities and the top head section can be fixed or removable.
AE style reactors datasheet- DIN 28136 Reactor type AE
BE style reactors datasheet- DIN 28136 Reactor type BE
CE style reactors datasheet- DIN 28136 Reactor type CE
What are the components of a Glass lined reactor?
Glass Lined Reactors consist of a main body, top section with connecting nozzles & man way, baffles, dip pipes, agitator with mechanical seal, tank outlet valve and jacket for thermal transfer. Smaller components such as bursting discs and sight glasses are also used frequently for pressure relief and visibility.
What are the advantages of glass lined reactors vs stainless steel reactors?
A key advantage is the range of chemistry that can be performed in a glass reactor. Stainless reactors are very good for a wide range of solvents and dissipate the static charge. However, they are limited when it comes to the presence of certain acids (Hydrochloric) and salts (Chlorides). Stainless steel reactors are generally less expensive.
What is a glass lining?
A glass lining is the application of a layer of glass via powder coating that is then heated in a furnace which then bonds to the metal of the vessel. The thickness and glass type & colour can vary but a general guide is 2mm thickness for most duties.
How do you inspect glass lined vessels?
In the main there are spark tests and related conductive tests. Also there is vessel entry visual inspection. Flexachem offer to test the vessels and reglass the vessel – generally speaking we can offer to re-glass most, if not all, major brands on the market today. The typical turnaround cost is 12-14 weeks from arrival at the factory.
Do you have questions or comments about receiving a quote, our products, solutions and services, and support? Contact us by filling out the form.
- Stephen White - Mob: 083 165 3830
- Michael Bradley (External) – Mob: 086 047 6178
- Ross O’Donovan – Tel: 021 461 7230
- Tel: 021 461 7200
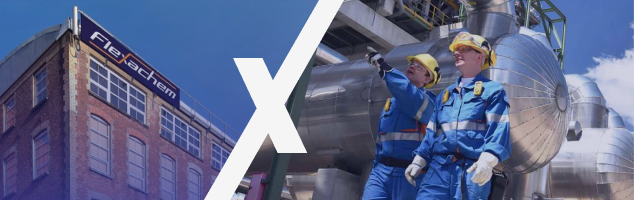
How can Flexachem help you?
Flexachem are partners with a leading manufacturer 3V Glasscoat, based in Italy. They are our partners for 5 years with many successful installations in the Irish pharmaceutical sector. 3V Glasscoat are part of the 3V Tech company who also manufacture filter dryers (3V Cogeim) and Evaporators (3V Mabo).
If you have a specific requirement around glass lined equipment, please contact one of our product specialists to discuss your application.