Filter Dryer
A filter dryer is an efficient way to separate solids from liquids, whether the product is the solid or liquid. The liquid slurry is transferred from reactors into the filter dryers and through mechanical agitation, pressure and heat – the resulting product is left behind or transferred onward.
- View All
- Actuation
- Chillers
- Heat Exchangers
- Instrumentation & Control
- Mechanical Seal
- Mixing Technology
- Other
- Process Equipment
- Pumps
- Sight Glasses
- Software
- Steam Systems
- Tank & Pipeline Ancillaries
- Tank Venting
- Valves
-
Mixing Technology3VTECH
Vacuum Drying
-
Mixing Technology3VTECH
Nutsche Pressure Filtration
How does a filter dryer work?
Typically in pharmaceutical applications, the end user will produce a slurry within which is the active ingredient. Separation can be carried out by having pressure above the liquids such as nitrogen blanketing and vacuum below the product to pull the liquid through a mesh. The dryer aspect allows the safe removal of impurities and drying the product without exposing the operator to possibly toxic products or impurities from the environment. The drying evaporates the solvents and concentrates the product as a cake within the filter. A mechanical agitator is used to assist the process
What is the nutsche filter principle?
This is an overview of the typical process involved. There are several steps along the way but can be summarised as filling, filtering, displacement washing, reslurring washing, smoothing, drying / cooling and discharging.
What are the advantages of using a filter dryer?
You have a safe and contained process to recover a product (liquid or solid) from your process that has the impurities removed.
Is there a difference between a filter dryer and a pressure filter dryer?
Filter dryers are solid – liquid separation systems that use a filter screen to promote the development of the filter cake. Use of nitrogen above the cake and of vacuum underneath the filter mesh, can improve the filtration process. Supply of a heating fluid to the vessel and agitator jackets in combination with vacuum inside the vessel, generates the appropriate conditions for solvent evaporation and, thus, for cake drying. Pressure is used above the slurry as a nitrogen blanket.
What is the difference between pressure, batch and continuous filtration?
Batch and continuous are the two filtration processes. Batch simply refers to the filtration of a fixed volume to completion and prepare for the next batch when ready. Continuous filtration is adopted where high throughput production in combination with relatively compact size equipment are desired. Continuous filters provide the benefit of a very low energy consumption and a fully sealed and contained construction. They meet the stringent requirements for operator safety and containment of toxic products.
The Flexachem supported brand, Cogeim, offers alternative filtration technologies for thick cakes combined with high pressure and for thin cakes combined with lower pressure conditions. Applications Bulk and final pharmaceuticals, Dyes and pigments, Agrochemicals, Fine Chemicals, Food and Plastics.
Which brands of filter dryers and vacuum dryers does Flexachem supply?
3V Tech’s Cogeim division has been a world-leading supplier of Solid-Liquid Separation equipment to the pharmaceutical, fine chemical and chemical industries for 40 years.
Flexachem is a leading distributor and we supply to the market 3V Cogeim filter dryers. Our end users have direct access to the factory specialists and have been in partnership with 3V Tech for 5 years.
What are the uses and applications for a filter dryer in Pharmaceutical?
The main function is liquid solid separation. Some applications typically include;
- Active Pharmaceutical Ingredients (API)
- Agrochemical products
- Extraction processes
- Purification processes
- Convection drying
- Hygroscopic products
What is the difference between a filter dryer and a vaccum dryer?
Vacuum is part of how the filter dryer works. The product is pulled through the fine mesh to leave the product or waste cake behind. The nitrogen blanket above the product will push from the other side. The vessel walls are heated to enable the evaporation of the solvents which can be recovered.
Watch the filter dryer in action for yourself.
If you have a specific requirement, please contact our Process Equipment Specialist to discuss your application in more detail.
Do you have questions or comments about receiving a quote, our products, solutions and services, and support? Contact us by filling out the form.
- Stephen White - Mob: 083 165 3830
- Michael Bradley (External) – Mob: 086 047 6178
- Ross O’Donovan – Tel: 021 461 7230
- Tel: 021 461 7200
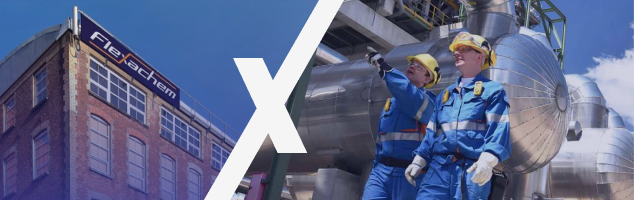