Double Mechanical Seal
A double mechanical seal is a type of mechanical seal with two primary seals or sets of faces, it can operate in various arrangements with a) a barrier (containment) between the sets of faces or b) a buffer (mixing).
The arrangements vary from:
- A Double Mechanical Seal (Barrier) – Dry => is a double seal where the barrier fluid is a gas.
- There are 2 specific types; Dry Running Contacting and Dry Running Non-contacting.
- View All
- Actuation
- Chillers
- Heat Exchangers
- Instrumentation & Control
- Mechanical Seal
- Mixing Technology
- Other
- Process Equipment
- Pumps
- Sight Glasses
- Software
- Steam Systems
- Tank & Pipeline Ancillaries
- Tank Venting
- Valves
-
Mechanical SealFlowserve
Lift Off and Dry Running (ML-200)
Some factors to consider when selecting a Double Mechanical Seal – Dry Running Contact;
- Barrier or buffer fluid is a gas
- Not available on Pumps
- Good for containment
- Good for preventing contamination
- Mechanical Seal face wear (debris well)
- Atex limits (seal face heat)
- General speed limits (seal face heat)
- Failure mode is generally stable for mixer seals
- Can be CIP’d/SIP’d but not great for seal life.
Some factors to consider when selecting a Double Mechanical Seal – Dry Running Non-Contact;
- Dry running non-contacting (or gas lift-off) – the barrier fluid is a gas
- Gas Usage rates are higher than contacting (issue for hard vacuum)
- Strict run-out tolerances – suitable for your machine?
- Fast rotation machinery (pumps, blowers, compressors) seals operate on hydrodynamic lift
- Slow rotation machines (mixers) operate on hydrostatic lift.
- No contact between faces, no wear during normal running
- Atex limits are much higher
- General speed limits are much higher
- Failure mode is generally catastrophic for inboard seal, quick shut off required.
- Beware of powders on mixer applications.
- Very good with solids, difficult liquids & all gases.
- Highest temperature and pressure running limits
- Can be SIP’d but MUST be dried in place.
2. A Double Mechanical Seal (Barrier) – Wet => is a double seal where the barrier fluid is a liquid. It is generally the most robust seal. It has a good pressure, speed and temperature capabilities.
Some factors to consider when selecting a Double Mechanical Seal – Wet lubricated;
- Wet lubricated – the barrier fluid is a liquid
- Very low leakage rates
- Barrier fluid must be compatible with product
- Run-out allowances are high
- Atex limits are high
- General speed limits are high
- Failure mode depends on speed and barrier fluid
- Can be SIP’d
3. A Double Mechanical Seal (Barrier) – Buffer (Mixing) => is a double seal where the barrier fluid is generally wet-lubricated type.
Some factors to consider when selecting a Double Mechanical Seal – Bottom Entry Seal;
- Bottom entry seal
- Generally wet-lubricated type
- Very Low leakage rates
- Run-out on bottom entry mixers is higher due to system instability
- Direct contact with product
Flexachem offer a full range of Flowserve Double Mechanical Seals:
If you have any query around how to install double mechanical seals for agitators or mixers or have some concerns around the seal failures, why not contact one of our mechanical seal specialists below to discuss it in more detail and find out how we can help solve your issues and get your process back up and running reliably again.
Do you have questions or comments about receiving a quote, our products, solutions and services, and support? Contact us by filling out the form.
- Chris Sheeran (External) – Mob: 087 755 9936
- Evan Twomey - 083 162 0251
- Miriam Adair - Tel: 021 461 7235
- Office Tel: 021 461 7200
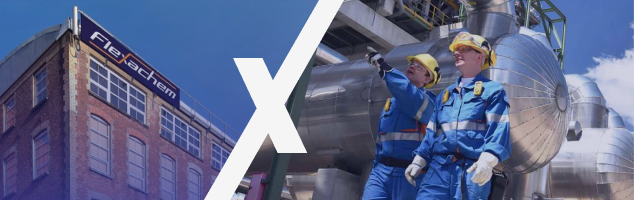