Mechanical Seal
A mechanical seal is a device used to effect a seal between a rotating or reciprocating part and a stationary part on rotating equipment i.e Pumps, Agitators, Mixers, Vessels etc.
The use of the word “seal” is a misnomer; as a mechanical seal is a restrictive flow path, that is either an angular or radial gap. The flow through this gap is generally so low it goes unnoticed if a liquid or inconsequential if a gas.
- View All
- Actuation
- Chillers
- Heat Exchangers
- Instrumentation & Control
- Mechanical Seal
- Mixing Technology
- Other
- Process Equipment
- Pumps
- Sight Glasses
- Software
- Steam Systems
- Tank & Pipeline Ancillaries
- Tank Venting
- Valves
Product categories
-
Mechanical SealFlowserve
HSH – Pusher Seal
-
Mechanical SealFlowserve
MixerPac 2568 – Top-entry Mixer Seal
-
Mechanical SealFlowserve
Flowserve Steel Vessel Seal
-
Mechanical SealFlowserve
Bearing Gard Isolator with electrical earthing
-
Mechanical SealFlowserve
Bearing Gard – Isolators
-
Mechanical SealFlowserve
Buffer Fluid Reservoirs
-
Mechanical SealFlowserve
Barrier Gas Panels
-
Mechanical SealFlowserve
EPD – Erosion Protection Device
-
Mechanical SealFlowserve
SLM 6200
-
Mechanical SealFlowserve
SLM 6100
-
Mechanical SealFlowserve
SLM 6000
-
Mechanical SealFlowserve
SLC
Download Now your guide on how to analyse Mechanical Seal failure & causes
How does a Mechanical Seal work?
A mechanical seal works by retaining a liquid or gas inside a rotating piece of equipment. Mechanical seals can be designed to prevent contamination of the process by the environment and prevention of leakage of the process into environment.
The basic components of a mechanical seal are a Rotating Part and a Stationary Part. The primary seal of a mechanical seal consists of a rotating face and a stationary face. The faces are kept lubricated by maintaining a thin film of fluid between each face. There is a very small gap between these 2 components which creates a restrictive flow path.
There are other components namely o-rings or gaskets which are used as secondary seals and hardware which is used to support the seal faces and to attach them to the rotating part (i.e shaft) and stationary part (i.e cover plate).
What are the types of Mechanical Seals?
- Single Seal => it consists of one primary seal and it seals from process to atmosphere.
- There is always some leakage either to atmosphere or into process depending on the process pressure.
- Double Seal (Barrier) => consists of two primary seals in various arrangements. There is a barrier fluid between the two primary seals which is at a higher pressure than the process. There is always some leakage of the barrier fluid in process & out to atmosphere. As long as barrier pressure is maintained there is no leakage of process to atmosphere or contamination of process by environment.
- Double Seal (Barrier) – Wet => is a double seal where the barrier is a liquid. It is generally the most robust seal. It has a good pressure, speed and temperature capabilities.
- Double Seal (Barrier) – Dry => is a double seal where the barrier fluid is a gas. There are 2 specific types; Contacting and Non-contacting.
- Gas Contacting Seal – the seal faces are in contact, the soft face wear acts as a lubricant. Low pressure, speed and temperature capabilities and possibilities of wear getting into the process.
- Gas Non Contacting Seal – the seal faces are NOT in contact. They are kept apart by a flow of gas between the faces. Good temperature, speed and pressure capabilities. If operated correctly their is no wear but care must be taken in order to minimise shaft run out.
- Component Seal => is where both the rotating & stationary hardware are connected separately to the pump/mixer.
- Cartridge seal => is where the rotating and the stationary hardware are pre-assembled before mounting onto the pump/mixer. Cartridge seals are much easier to fit & maintain compared to the component seal.
What is the difference between a Shaft Seal and a Lip Seal?
A shaft seal is any type of seal which seals a shaft and stationary part e.g o-ring, lip seal or mechanical seal etc
A lip seal is a specific type of seal, it is a radial seal, where the part that seals against the rotating surface is a narrow cross section, soft material i.e the lip and it is made from an elastomer or non-elastomer material with a backup spring. Most commonly used to seal bearings in Mixers/Agitators. A lip seal rotates too quickly to be used on pumps.
What is a Barrier Fluid?
A barrier fluid is any gas or liquid which is used to pressurise a double mechanical seal. It must be compatible with the process, generally non-toxic and a good lubricant.
Check out our blog post on barrier fluid to find out more.
What is the barrier fluid pressure for water or other?
The barrier pressure should be above the process pressure.
In the case of a pump seal, this is set to a certain value above the stuffing box/seal chamber pressure. For this value, please consult seal IOM.
The seal chamber pressure needs to be calculated as it varies with pump type/impeller type/suction pressure/discharge pressure etc
Please consult the pump manufacturer/distributor for guidance on these calculations for mixer seals, the barrier pressure is set at a certain value above the maximum vessel pressure.
What are Mechanical Seal Faces?
The primary seal of a mechanical seal is made up of 2 seal faces where these two parts meet is where the seal gap is located. The mating surface of the seal face is machined to a very tight tolerance.
A seal face can be made from either soft or hard materials. A soft seal face is generally a wearing material.
Mechanical Seals vs Packing?
Packing is a material that is stuffed between a rotating shaft and a stationary part gland to maintain pressure. Packing is a low cost alternative to mechanical seals.
However, the advantages of mechanical seals over packing is that they have;
- a lower leakage by a factor of 103
- there is no shaft wear,
- they are more robust with higher speeds, pressures & temperatures.
- better chemical compatability and are longer lasting.
What is a Mechanical Seal leak test procedure?
There are a number of bench test procedures for pressure testing mechanical seals, the most common one is API 682 which Flowserve use.
– API 682 – Pressurised seal to 25 psig.
– Maximum pressure loss is 2psi/5 mins.
Do you have questions or comments about receiving a quote, our products, solutions and services, and support? Contact us by filling out the form.
- Chris Sheeran (External) – Mob: 087 755 9936
- Evan Twomey - 083 162 0251
- Miriam Adair - Tel: 021 461 7235
- Office Tel: 021 461 7200
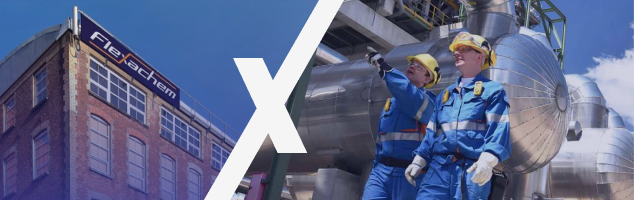
How we can help you?
Flexachem provides a full range of Flowserve Mechanical Seals.
We supply mechanical seals into the pharmaceutical, bio-technology, chemical processing, mineral and ore processing, semi-conductor and general industries.
Depending on your particular application, if you are looking mechanical seals to suit a pump application; Mechanical Seal for Pumps, or if you are trying to source mechanical seals for an agitator or tank mixer; Mechanical Seal for Agitator, or perhaps you have a hygienic application in mind, take a look at our range of Mechanical seal for Hygienic & Aseptic applications.
We also provide Seal Support Systems – reservoirs, barrier systems, piston transmitters, gas panels, seal coolers, circulators and fill carts.
Our Mechanical Seal specialists can advise you on the appropriate selection of a seal support system which will deliver years of reliable service and operating cost savings in the longer term.
Our Flowserve heritage mechanical seal brands include:
Durametallic Seals specialist in Pharma, chemical and API seals.
Pacific-Wietz Seals specialist in Compressor and Pharma seals.
Borg-Warner Seals (part of BWIP – Borg-Warner Ingersall (Dresser) Pumps) specialist in API and gearbox seals.
Five-star Seals specialist in Pump seals and marine applications.
Pac-Seals specialist in OEM and specialty seals.
If you have any query around how to install mechanical seals or have some concerns around seal failures, why not contact one of our seal specialists below to discuss it in more detail and find out how we can help solve your issues and get your process running reliably again.