
Kenics Shell & Tube Heat Exchanger
Kenics® Static Mixer technology, available exclusively in Kenics® Heat Exchangers, offers the highest available coefficients for fast, uniform heat transfer. Capable of reliable operation in a wide range of process applications, including those in the polymer, plastic, and food and beverage industries, Kenics Heat Exchangers require less space, less energy and less residence time than standard designs.
Static Mixing Technology
The Kenics Heat Exchanger consists of a continuous string of static mixer elements within each heat exchanger tube. Fluid flow is directed radially toward the pipe walls and back to the element, regardless of velocity. Additionally, momentum reversal and flow division also contributes to the mixing efficiency. All processed material is continuously and completely intermixed to eliminate radial gradients in temperature, velocity and material composition. As a result, Kenics Heat Exchangers provide predictable, controlled mixing, and the most efficient form of thermal transfer available today.
Efficient Heat Exchanger Design
By using Kenics Static Mixer elements in each heat exchanger tube, the film build-up commonly associated with laminar flow empty tubes is significantly reduced. Process fluid is continuously pushed from the center of each tube, to the wall and back to the center, eliminating thermal gradients and boosting the inside film coefficient.
Kenics Static Mixer elements produce a more uniform, consistent transfer process, with three to seven times greater
- Specifications
- Technical Data
- Advantages
- Industries
- Applications
- Contact
Specifications
Operating Parameters:
- Flows to 565 m³/h (2500 gpm)
- Heads to 110 m (350 ft)
- Pressures to 17 bar (250 psi)
- Temperatures from -30°C (-20°F) to 90°C (200°F)
Shaft Metallurgy Options:
- 316 SS
- Alloy 20
- Hastelloy
- Titanium
Features:
- Full basket strainer
- NEMA in-line motor
- Fiberglass mounting plate
- Tapered “Polygon” impeller drive
- “Pull-out” bearing retainers
- Level controls
Options:
- Simplex and duplex pit covers
- Float switches
- Particulate separators
- Non-metallic lubrication lines
- Tailpipe
Technical Data
- Engineered Polymer Composite Construction offers cost-effective corrosion-resistance, is lightweight, non-galling, non-sparking, and non-conductive.
- Unitized Case with Integrally Molded Flanges at the suction and discharge nozzles, fully gusseted for structural soundness.
- Externally Adjustable, Semi-Open Impeller provides consistently high efficiencies and minimizes maintenance.
- Shaft/Bearing System operates below the first critical speed for less shaft whip and longer bearing life.
- Bearings can be lubricated by external flush or self-lubricated by the pump fluid.
- Single-Piece Column is lightweight, filament-wound, reinforced fiberglass composite for strength and rigidity.
Advantages
- Lightweight and corrosion-resistant due to engineered polymer composite construction.
- High efficiency and minimal maintenance with externally adjustable impeller.
- Long bearing life with low shaft whip and flexible lubrication options.
- Robust construction with unitized case and reinforced single-piece column.
Industries
- Leaching Acid
- Chemical and Liquor
- Caustic and Chlor-Alkali
- Bleach Chemicals
- Auxiliary
- Acid Transfer
- OEM
- Water Treatment
- Water Supply and Distribution
- Wastewater Collection and Treatment
- Polymers
- Plating, Galvanizing and Other Coatings
- Pharmaceuticals
- Automotive and Aircraft
Applications
- Corrosive Services
- General Purpose
- Water Treatment
- Pulp and Paper
- Chemical Processing
- Utility
- Metal and Steel Industry
- Pollution Control
- Plating
Contact our Pump Specialist Team
- Andrew Bishop - tel: 083 089 1204
- Phil Soltan (External) – mob: 086 185 3782
- Adrian McSweeney – tel: 021 461 7212
- Paul-Fox Morris – tel: 021 461 7231
- Una Long (Pump & Service Support) – tel: 021 431 7200
- Tel: 021 461 7200
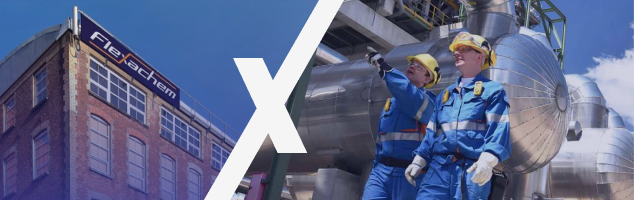
-
Heat ExchangersKelvion
Brazed Heat Exchangers
-
Mixing TechnologyKenics
Kenics Heat Exchangers
-
Heat ExchangersKelvion
Free Flow Plate Heat Exchangers
-
Heat ExchangersKelvion
Finned Tube Heat Exchangers
-
Heat ExchangersKelvion
GWH Series Brazed Plate Heat Exchanger
-
Heat ExchangersKelvion
GVH-Series Brazed Plate Heat Exchanger
-
Heat ExchangersKelvion
GK-Series (ConBraze) Brazed Plate Heat Exchanger
-
Heat ExchangersKelvion
GBS-Series Brazed Plate Heat Exchanger