
Kenics KM Static Mixers
Mixing Technology
Kenics
Send Enquiry
Kenics KM Series Static Mixers utilize a patented helical mixing element to direct the flow of material radially towards the pipe walls and back to the center. The alternating right- and left-hand elements create additional velocity reversal and flow division, enhancing mixing efficiency. This design ensures continuous and complete mixing, eliminating radial gradients in temperature, velocity, and material composition. Kenics Static Mixers are proven to maximize mixing efficiency without the energy waste and material blockage typical of more restrictive motionless mixers.
- Specifications
- Technical Data
- Advantages
- Industries
- Documents
- Contact
Specifications
- Sizes: 3/16″ to 120″
- Material Options:
- Carbon steel
- 304 Stainless Steel
- 316 Stainless Steel
- Alloy 20
- Monel 400
- Hastelloy C-276 & B2/3
- Titanium
- Nickel 200
- Inconel 600/625
- PTFE
- PVC
- CPVC
- FRP
- Other materials available upon request
- Geometry: Limited to round pipe, tubing, or duct
- Retention Types: Welded, removable, edge-sealed
Technical Data
- Principles of Operation:
- The patented helical mixing element directs material flow radially towards the pipe walls and back to the center.
- Alternating right- and left-hand elements induce additional velocity reversal and flow division.
- Ensures continuous and complete mixing, eliminating radial gradients in temperature, velocity, and material composition.
- Mixing Applications:
- Turbulent Blending: Rapid mixing with circular patterns that reverse direction at each element intersection.
- Laminar Blending: Alternating helical elements continually divide, stretch, and reorient the flow stream with minimal pressure drop.
- Liquid/Liquid Dispersion: Uniform turbulent shear field disperses immiscible liquids with a narrow drop size distribution.
- Gas Liquid Dispersion: Gases are incorporated into turbulent liquids, enhancing mass transfer rates for absorption or reaction.
- Extrusion: Thermogenizers blend thermal gradients and supplemental color/additive blending.
Advantages
- Efficient Mixing: Patented helical design maximizes mixing efficiency with minimal energy waste and no material blockage.
- Versatile Applications: Effective for turbulent and laminar blending, liquid/liquid dispersion, gas/liquid dispersion, and extrusion.
- Material Variety: Available in a wide range of materials to meet various requirements and environmental conditions.
- Customizable Sizes: Accommodates sizes from 3/16″ to 120″ and multiple retention types.
Industries
- Chemical Processing
- Pharmaceutical
- Food and Beverage
- Water and Wastewater Treatment
- Oil and Gas
- Plastics and Polymers
Documents
Contact our Process Equipment Team
- Stephen White - Mob: 083 165 3830
- Michael Bradley (External) – Mob: 086 047 6178
- Ross O’Donovan – Tel: 021 461 7230
- Tel: 021 461 7200
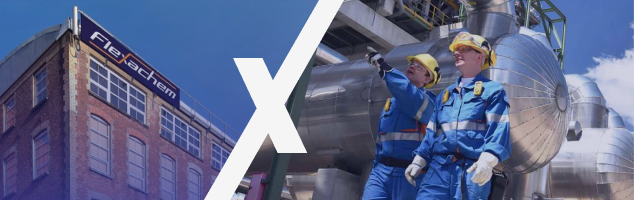
-
Mixing TechnologyKenics
Kenics HEV Mixer
-
Mixing TechnologyKenics
Kenics Heat Exchangers
-
Mixing TechnologyKenics
Kenics KMX Static Mixer
-
Heat ExchangersKenics
Kenics Shell & Tube Heat Exchanger
-
Mixing TechnologyKenics
WVM Kenic Static Mixers
-
Mixing TechnologyChemineer
WVM Static Mixers
-
Mixing TechnologyGreerco
Greerco Pipeline Mixers
-
Mixing TechnologyFlowserve
IBC Mixers