
Cora Double Valve Gasket
The CORA Double Valve Gasket was conceived to control the dosing as well as packaging of powder product during the filling processes. It consists of a butterfly valve with a central rotor and located on the bottom of machine process outlets driers or bins. This valve was designed to be an automatic and programmable weight system.
How the valve functions:
1. Heavy dosing: The butterfly opens and discharges 95% of the weight. When the bulk weight limit is obtained closes.
2. Fine dosing: When the butterfly closes, the central rotor begins trickle feed until the total weight of the product with an accuracy which varies from ± 20 gr to compliance with the characteristics of a treated product. The fine dosing pockets of the rotor can be numbered and the volume created would be based on customer requirements. The most common application is the continuous liner dosing system, conceived by CO.RA., which allows the discharge of product inside a polyethylene liner as well as the filling of bags in a closed cycle, controlling the weight with more accuracy.
The Cora Double Valve Gasket is a variant of the Double Valve and has a seal between the butterfly and the dosing rotor. This solution allows the valve to work in applications with pressure up to 0.5 bar and with less product leakage during the discharge cycle. Following numerous tests, CORA will certify that it is possible to use this type of valve in environments classified PBOEL 4.
Rotor and Dosing Accuracy:
The dosing accuracy of the DOUBLE VALVE and VALVE GASKET is ± 50 grams with 90% of pharmaceutical products. CO.RA. has found a solution to obtain higher dosing accuracy to meet customer requirements. The solution consists of customizing the volume and number of pockets so it can reach a dosing accuracy of ± 10. In these cases, it is necessary to “fine tune” the process by running tests using the customer’s product. These tests can be carried out using either a DOUBLE or a DOUBLE VALVE GASKET that are available as CORA’s Technology Center.
- Specifications
- Technical Data
- Advantages
- Industries
- Applications
- Contact
Specifications
Operating Parameters:
- Flows to 565 m³/h (2500 gpm)
- Heads to 110 m (350 ft)
- Pressures to 17 bar (250 psi)
- Temperatures from -30°C (-20°F) to 90°C (200°F)
Shaft Metallurgy Options:
- 316 SS
- Alloy 20
- Hastelloy
- Titanium
Features:
- Full basket strainer
- NEMA in-line motor
- Fiberglass mounting plate
- Tapered “Polygon” impeller drive
- “Pull-out” bearing retainers
- Level controls
Options:
- Simplex and duplex pit covers
- Float switches
- Particulate separators
- Non-metallic lubrication lines
- Tailpipe
Technical Data
- Engineered Polymer Composite Construction offers cost-effective corrosion-resistance, is lightweight, non-galling, non-sparking, and non-conductive.
- Unitized Case with Integrally Molded Flanges at the suction and discharge nozzles, fully gusseted for structural soundness.
- Externally Adjustable, Semi-Open Impeller provides consistently high efficiencies and minimizes maintenance.
- Shaft/Bearing System operates below the first critical speed for less shaft whip and longer bearing life.
- Bearings can be lubricated by external flush or self-lubricated by the pump fluid.
- Single-Piece Column is lightweight, filament-wound, reinforced fiberglass composite for strength and rigidity.
Advantages
- Lightweight and corrosion-resistant due to engineered polymer composite construction.
- High efficiency and minimal maintenance with externally adjustable impeller.
- Long bearing life with low shaft whip and flexible lubrication options.
- Robust construction with unitized case and reinforced single-piece column.
Industries
- Leaching Acid
- Chemical and Liquor
- Caustic and Chlor-Alkali
- Bleach Chemicals
- Auxiliary
- Acid Transfer
- OEM
- Water Treatment
- Water Supply and Distribution
- Wastewater Collection and Treatment
- Polymers
- Plating, Galvanizing and Other Coatings
- Pharmaceuticals
- Automotive and Aircraft
Applications
- Corrosive Services
- General Purpose
- Water Treatment
- Pulp and Paper
- Chemical Processing
- Utility
- Metal and Steel Industry
- Pollution Control
- Plating
Contact our Valve Specialist Team
- Brendan Merrigan (External) – mob: 087 2598124
- Vicki McGrath – tel: 021 461 7207
- Brian Barry – tel: 021 461 7211
- Tim Quigley – tel: 021 461 7209
- Ross O’Donovan – tel: 021 461 7230
- Shauna O’Connor – tel: 021 461 7237
- Cathal Hannon - Tel: 021 461 7200
- Office - tel: 021 461 7200
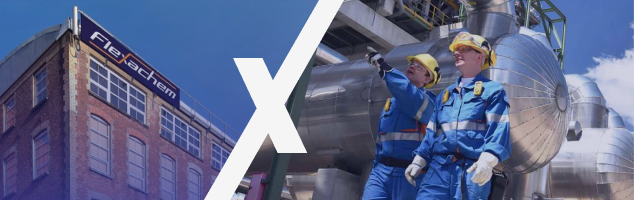
Related Products
-
ValvesCORA
Cora VR8V Valve
-
ValvesCORA
Cora Rotary Valve
-
ValvesCORA
Cora Double Valve ®
-
ValvesCORA
CORA Tablet Valve
-
ValvesCORA
CORA Sole Valve
-
ValvesCORA
CORA HR Crusher Valve
-
ValvesCORA
CORA Rotary Tablet Valve
-
ValvesCORA
CORA SRF Valve