Actuation
An actuation valve, is a type of valve, where the means of opening and closing the valve is carried out by a controlled device (Actuator), whether its mechanical or electrically driven, this can be Pneumatic, Electric or Hydraulic, each depending on the field of operation, and fall into two different categories, Rotary and Linear.
- View All
- Actuation
- Chillers
- Heat Exchangers
- Instrumentation & Control
- Mechanical Seal
- Mixing Technology
- Other
- Process Equipment
- Pumps
- Sight Glasses
- Software
- Steam Systems
- Tank & Pipeline Ancillaries
- Tank Venting
- Valves
-
ActuationFlowserve
Logix 520 MD+ Digital Positioners
-
ActuationFlowserve
SX-Series Stainless Steel Actuator
-
ActuationFlowserve
P5 Pneumatic Positioner
-
ActuationFlowserve
F5 Feedback System
-
ActuationFlowserve
EP5 Electro Pneumatic Positioner
-
ActuationFlowserve
PMV D3 Digital Positioner
-
ActuationFlowserve
3400IQ Digital Positioner
-
ActuationFlowserve
3200 Digital Positioners
-
ActuationFlowserve
Apex 6000 Positioner
-
ActuationFlowserve
APEX 8000 Positioner
-
ActuationFlowserve
APEX 5000 Pneumatic Positioner
-
ActuationFlowserve
APEX 4000 Positioner
What is the function of actuator valve?
The main function of an actuator valve is to control the flow of media via logical functions using a semi, or fully automated system, which is normally controlled via a PLC or other logic function software. Many different types of actuator valves are available on the market, most types of valves can accommodate some form of an actuator to allow the remote switch, such as; ball valve, butterfly valve and globe valve.
What is the difference between Hydraulic, Pneumatic, and Electric actuators?
A Hydraulic Actuator uses a fluid for this driving media, which is normally a mineral oil, and will have several components to allow the correct operator of the Hydraulic Actuator, this will include;
- Hydraulic pump
- Reservoir
- Flow controllers and or Regulation
- Filtration
- 3 port 2 position for single acting actuation
- 5 port 2 position for double acting actuation
- 5 port 3 position for double acting-controlled position, with Centre closed
- Hydraulic piping
- Actuator (Rotary or Linear)
- Positioner
A Pneumatic Actuator, probably the most common form of actuation, and uses the media of compressed air, depending on factory standard around 5-7bar or 0.5-0.7Mpa, and will include the following items:
- Compressor
- Flow controllers and or Regulation
- Filtration
- 3 port 2 position for single acting actuation
- 5 port 2 position for double acting actuation
- Pneumatic piping, Flexibly or solid
- Actuator (Rotary or Linear)
- Positioner
An Electric Actuator use the means of electricity, mains or stored supply like a battery pack for remote application:
- Electrical energy, normally 24Vdc, but can vary depending on installation and customer needs.
- Electrical motor or Solenoid
- Gearbox
- Positioner
What is a Linear actuator?
A linear actuator converts energy from one of the media’s, into a straight-line motion, normally in the vertical application, but can also be in the horizontal, typical for Gate or Globe valves.
What is a rotary actuator?
A rotary actuator converts energy from given media’s to rotary motion, for use on Ball and Butterfly valves.
What is the difference between an actuator and an actuation valve?
An Actuator is the mechanical or electrical component used to covert energy into motion, e.g Linear or Rotary Actuators, the actuation valve is the component being controlled by the driving or turning motion of the Actuator.
What is the difference between an actuator and a solenoid?
An actuator is normally the chamber that holds the compressed air, or hydraulic fluid in turn creates the force depending on the bore of the actuator, the bigger the bore, the greater the force.
The solenoid valve is the control function of the force diverter, when switch will divert the path of flow from one port to another resulting in the Actuator moving to extend or retract if linear, and clock wise or anti clock wise if rotary.
How do you test an actuation valve?
An actuation valve is tested by connecting it to a means of energy, such as compressed air, or electric power, and carrying out a calibration sequence to ensure it meets the parameters required.
What causes an actuator to fail?
Actuators can fail from some of the following reasons, such as;
- Incorrect sizing
- Incorrect installation
- Over pressurising the system
- Life cycle
- Mechanical obstructions
- Spicks in electricity
- Component failure
Do you have questions or comments about receiving a quote, our products, solutions and services, and support? Contact us by filling out the form.
- Brendan Merrigan (External) – mob: 087 2598124
- Vicki McGrath – tel: 021 461 7207
- Brian Barry – tel: 021 461 7211
- Tim Quigley – tel: 021 461 7209
- Ross O’Donovan – tel: 021 461 7230
- Shauna O’Connor – tel: 021 461 7237
- Cathal Hannon - Tel: 021 461 7200
- Office - tel: 021 461 7200
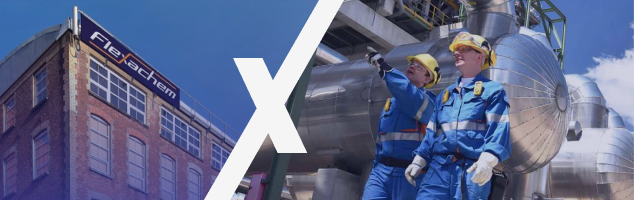
How can Flexachem help you?
Flexachem offers actuation valve packages and a selection of switchboxes/positioners. Please contact one of our valve product specialists, if you would like to enquire about our in-house service for assembling actuation valve packages which is carried out by our qualified trained technicians in our clean controlled environment area within our Service Centre.
Flexachem supply and support the following brands of Actuation Valves;
ABO, Norbro, Kammer, Valtek, Inoxpa and PBM
Positioners;
Logix and PMV
If you would like to find out more about our full range of actuation valve packages, why not speak to one of our valve specialist team?